3, composition and working principle of
This company produces the filter press is a mechanical, electrical and fluid
in the body, the level of advanced technology, the separation of mechanical
products. It consists of five main components: the frame parts, filter parts
(plate / box, cloth), pull board parts, hydraulic parts and electric control
part. According to user requirements can also increase the access fluid devices.
Specific structure shown in Figure 1.
1, rack part of the
The main body of the machine part is the machine
used to support the filter body to connect to
other components. It is mainly from the thrust
plate, pressed board, cylinder body and the main
beam and so on parts. The machine work, the cylinder
piston to promote the body's pressed board, pressed
board and will be located between the thrust
plate filter, filter cloth pressed to ensure
that with the pressure of slurry pressure filters
in the filter indoors.
2, filter part of the
Filtering in part by a certain order in the main beam of the plate / box
and caught in the plate / filter cloth between the composition, plate /
frame and a white cloth are arranged to form a number of separate filtering
units -- - Filter Room (see Figure 2: filtering and washing flow chart).
Filtering the beginning, the slurry feed pump driven by the thrust plate
of the feed port into the filter room, and by the pressure generated by
the feed pump to filter. As the filter cloth to retain the role, so that
solid particles remain in the filter cake formed indoors, the filtrate
from the tap (free flow) or a fluid valve (undercurrent) emission (see
Table 1 Tap specifications). For washing cake, may be thrust plate washing
mouth pass into the washing water for washing of the cake; If you need
a lower moisture content of the cake, the same may pass into the compressed
air from the mouth wash through the cake layer, in order to remove the
part of the filter cake moisture (for UK models).
The use of the filter press process, the choice of filter cloth filter
effectiveness, efficiency plays a key role. Common market, filter cloth,
ownership of the materials are mostly man-made chemical fiber, can be broken
down as polyester, polypropylene, polyvinyl alcohol, polyamide and a few
species; also have the use of cotton and other natural fiber materials
made of silk cloth. Its physical and chemical properties of different materials
such as acid degree, alkali degrees, wear resistance, conductivity, mechanical
strength and other technical indicators have large differences. Cloth weaving
methods also varied widely, the extent of thin fibers, cloth and thickness
also have a direct impact on the performance of filter cloth. Slurry to
be filtered, the solid content ratio, particle size, chemical composition,
etc. are also vastly different, in order to achieve better filtering effect
and high filtration efficiency, filter cloth should be in the selection
of the combination of the two taken together, a reasonable matching, can
only obtain the best economic results.
The performance characteristics of filter cloth can be in the table below:
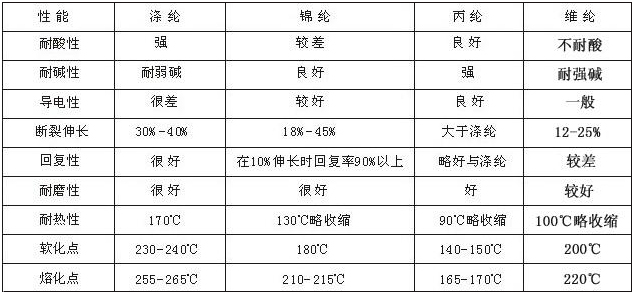
The company can select and process for the user on behalf of all kinds
of filter cloth.
Note:
① Polyester does not resistant to concentrated sulfuric acid and heated
between the acid;
② PP can not be resistant to chlorine acid, concentrated nitric acid and
other strong oxidizing acids, concentration of caustic soda, concentrated acetic
acid, propionic acid and chlorinated hydrocarbons such as incense. In addition,
the commonly used filter media including cotton cloth, non-woven fabrics, screen,
filter paper with microporous film, based on actual filtering request. If your
organization needs technical service in this area, please contact our company
(0571-86380607 86.37005 million).
3, pull board part of the
(1) Automatic drawing board part of the
Automatic pull plate in part by the hydraulic motors, mechanical hand,
transmission and suspension devices so on. Hydraulic motor driven chain
drive which will stimulate the hand movement, will be opened one by one
plate. Robot relies on the automatic change to the time relay PLC programmable
controller set time (2-3 seconds) to control. Suspension device can control
the drawing board at any time during the stop, into the action, to ensure
that agencies pull plate pull plate smooth realization of discharge.
(2) Manual pull board part of the
Followed by use of manually pulling plate discharge.
4, hydraulic part of the
Part is driven hydraulic clamping plate clamping or release plate of the
power plant, equipped with piston pumps and various control valves. Clamping
plate, it will be "Operation / packing / Pull Plate" switch pull to the "operation" position,
press the "pressed" button, electric start, the piston rod forward,
clamping plate; when the oil pressure rises to the upper limit of electric
contact pressure gauge, the electric contact pressure gauge connected to the
pump shut down the ceiling; In this case, the "action / packing / Pull
Plate" switch pull to the "packing" position, filter press that
is entered automatically packing state; When the hydraulic electric contact
pressure gauge it is set down to the lower limit, the piston pump to restart
the work required to ensure that filtration pressure; return, it will be "Operation
/ packing / Pull Plate" pull switch to the "operation" position,
press the "return" button, electric start, rod drive return pressed
board, filtering release, automatic drawing board for models, pull board, will "operate
/ packing / Pull Plate" switch pull to "pull board "position,
press the" pull sheet "button, pull board automatically reciprocating
pull plate, when the last one finished drawing board, installed in the thrust
monoblock Main beam trip switch was activated, pull board device back to the
starting position when the trigger limit switch automatically stops.
5, electric control part of the
Electric control part of the whole system control center. See the specific
principle of the electrical system diagram.
|