|
Powder knowledge |
Powder survey
Powder coating is a kind of new pure solid coating without any solvent. It has two types: thermoplastic powder coating and thermosetting powder coating.
The powder coating is made from special resin, additives, firming agent and some other agents through some special crafts. In common temperature, it is stable, decorative and corrosion resistant.
Characters:
1, Nontoxic, no solvent and no volatile toxic substance. It is fully accorded with the National Green Standards.
2, The utilizing rate can reach above 99%.
3, It does not need bottom painting with high productivity and low cost.
4, It has good intensity and toughness.
|
In the recent 20years, powder coating industry is developed a great deal. The reasons are as follow:
1. The development of powder coating new prescription;
2. The development of powder coating advanced equipments and vrafts.
Compared to the liquid coating, the powder coating has excellent durability, abrasion resistant, corrosion resistant, scratching resistant, chemical resistant. The surface luster is stable, unfading.
The green advantage is also a key factor for the liquid coating to convert to powder coating. The powder coating does not have solvent without any volatile substance. Using powder coating does not need ventilation, filtration and solvent reclaiming, but the liquid coating need.
|
Economical factor:
The development of powder coating material and equipments study reduces the cost a great deal. The total cost of powder coating execution is lower than that of common coating. After some researching institutes’ study, the cost of powder coating is a little higher than that of liquid coating, but the execution cost is lower.
The advantages of powder coating system are green, high-efficient, environment friendly, and low labor cost. And the real cost saving of powder coating is up to customers’ different requirements.
|
Powder coating execution crafts
The powder coating has two kinds of crafts: static spraying craft and fluidization coating craft.
|
(1) Static spraying craft
The powder coating static spraying is the mixing of powder and air. 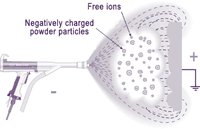
The static spraying gun can decide the spaying direction of powder, control deposition speed, control the size of image, figure and spraying density. The spraying gun can be manually controlled, or controlled by other automotive equipments.
The spraying gun has different designs, and different factors are how to make the guns take static. In some circumstances, the powder takes static depending on friction, which can keep the powder forming smooth coating on the surface of the parts, and also can improve the indention of the surface.
The thickness of coating is up to chemical property, pre heating temperature and sticking time. For the cool products, the thickness is always 1.5- 5.0 mil. (37.5 - 125 μm). But for heating products, the thickness is always 20-25 mil. (500 - 625 μm).
|
Fluidization coating craft
Fluidization coating craft is a simple soaking coating craft with common way and static way. In common craft, there are many holes in the fluidization equipment. The air below the hole board will evenly rising, and form the air and powder blending. The blending is like boiling liquid, and form continuous coating with melting powder.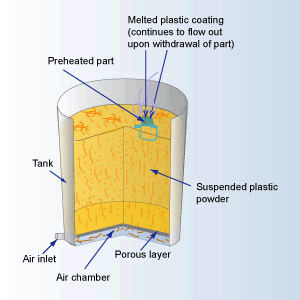
It can be used in the complex products. The thickness of coating can be 3-10 mil. (75 - 250 μm), and for the heating products, it can be 100 mil.(2500 μm).
|
Static fluidization coating craft
In static fluidization coating craft, the powder atom can take static. And the atoms will exclude each other, and form cluster powder. The powder thickness controlling of coating is like the static spraying way.
The advantages of static fluidization craft are:
(1), It does not need pre heating.
(2), For the small part, it can coat speedily.
|
Powder coating solidifying
For the thermoplastic powder, the heating is to form continuous film, but for thermosetting powder, it needs further heating to solidify film. The general powder coating solidifying ways are: convection, infrared radiation, infrared radiation and convection and ultraviolet radiation solidifying.
The convection oven can be heated by electricity or gas. The hot air encircles the part to reach given temperature. The ultraviolet can solidify the powder coating in several seconds.
The infrared oven also can be heated by gas or electricity, and the energy can be absorbed by powder. After some time radiation, powder can flow and solidify.
Infrared radiation and convection are generally divided into two zones. The first is infrared zone, and the other convection zone. The former one is to speedily melt the powder, which can quickly absorb infrared, and the latter is to make the part from the Zone 1 fully solidified.
|
Heating/Solidifying |
Temperature
( ℃ ) |
Solidifying time
(min) |
Basic material |
Common thermosetting powder coating |
Convection |
140-220 |
30-15 |
Metal |
Infrared radiation and convection |
140-220 |
25-10 |
Metal |
Infrared radiation |
160-250 |
15-1 |
Metal |
Ultraviolet solidifying powder coating |
Infrared/Convection (1-2min) and ultraviolet radiation solidifying(s) |
90-120 |
3-1 |
Metal,wood,plastic and others |
|
|
|
|